>>Limit the hydrolysis degradation of the viscosity.
>>Prevent increasing AA levels for materials with food contact
>>Increasing the capacity of the production line up to 50%
>>Improvement and make the product quality stable-- Equal and repeatable input moisture content
>>There are three P.I.D temperature control zones, and the crystal drying temperature can be set according to the characteristics of the raw materials.>>Rotary working style can be act as mixer. You can feed the percentage PET Chips and recycled pellets to our Infrared crystal dryer directly, it will mix the material automatically
Experienced engineer will make the test. Your employees are cordially invited to participate in our joint trails. Thus you have both the possibility to contribute actively and the opportunity to actually see our products in operation.
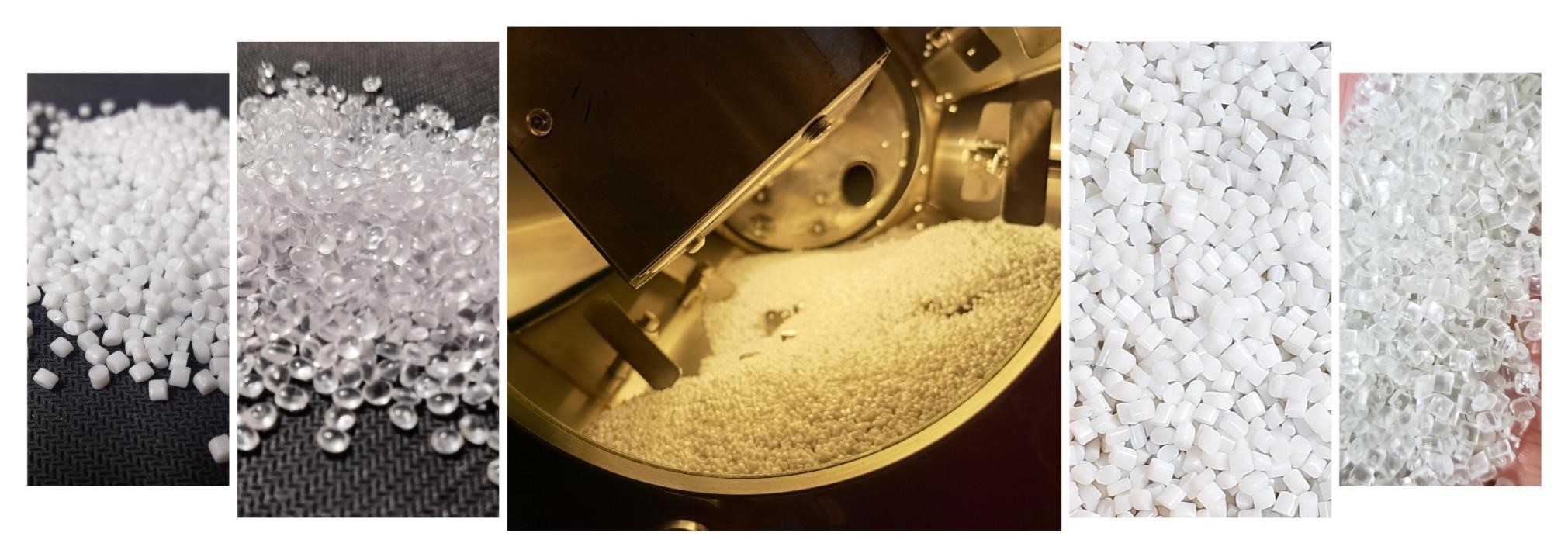
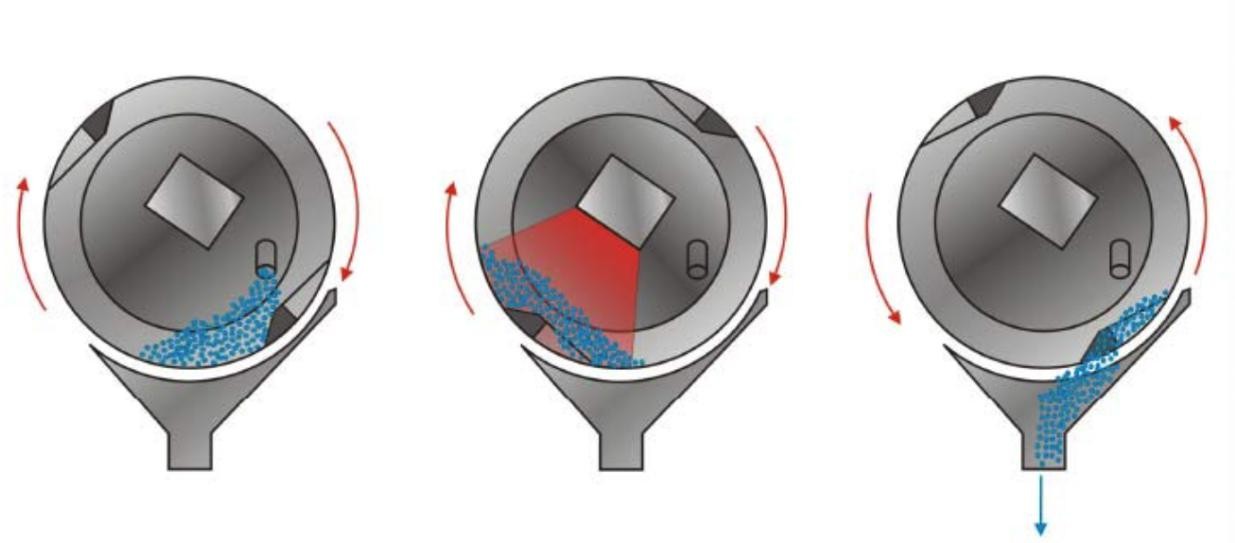
Feeding/Loading
Dry& Crystallization Processing
Discharging
>>At first step, the only target is to heat up the material to a preset temperature.
Adopt relatively slow speed of drum rotating, the Infrared lamps power of the dryer will be at a higher level, then the PET pellets wili have a fast heating till the temperature rises to the preset temperature.
>>Drying &Crystallizing step
Once the material gets to the temperature, the speed of the drum will be increased to a much higher rotating speed to avoid the clumping of the material. At the same time, the infrared lamps power will be increased again to finish the drying. Then the drum rotating speed will be slowed down again. Normally the drying process will be finished after 15-20mins. (The exact time depends on the property of material)
>>After finishing the drying processing, the IR Drum will automatically discharge the material and refill the drum for the next cycle.
The automatic refilling as well as all relevant parameters for the different temperature ramps is fully integrated in the state-of-the-art Touch Screen control. Once parameters and temperature profiles are found for a specific material, theses settings can be saved as recipes in the control system.
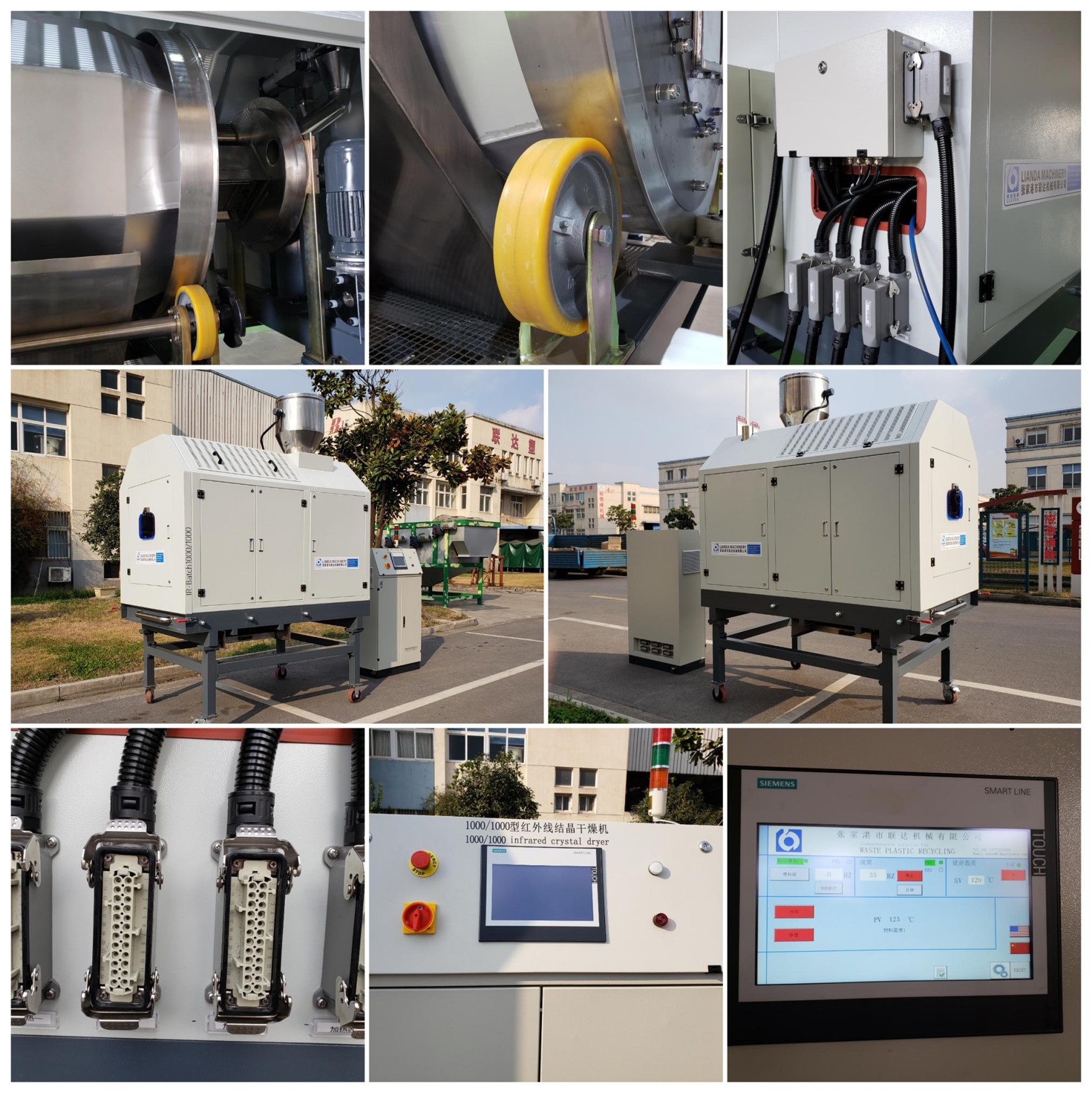
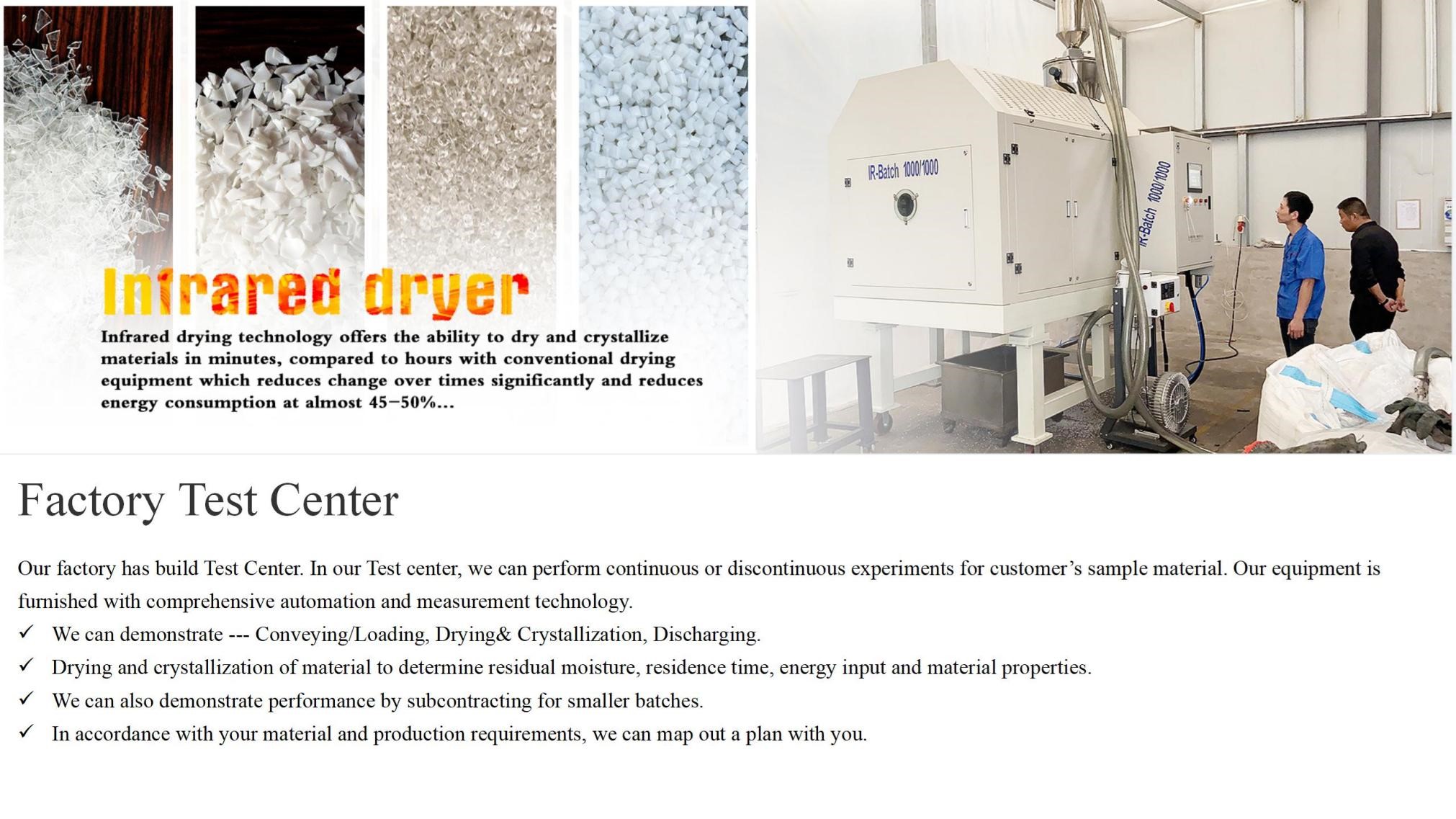
>> Supply Experienced engineer to your factory to help installation and material test running
>> Adopt aviation plug, no need to connect the electrical wire while the customer get the machine in his factory. To simplify the installation step
>> Supply the operation video for installation and running guide
>>Support on line service>> Dry &Crystallize PET Chips/Flake/Pellets in 20mins at 30ppm by saving 45-50% energy cost.
- Up to 60% less energy consumption than conventional drying system
- Uniform crystallization
- No pellets clumping & stick
- Crystallization colour Milk white
- Carefully material treatment
- Instant start-up and quicker shut down
- Independent temperature and drying time set
- No segregation of products with different bulk densities
- Easy clean and change material
How to Maximize product added value of R-PET Pellets/ PET Pellets made by Bottle flake by Infrared crystallization Dryer?
1 | Uniform crystallization ,high in crystallization rate Crystallization colour: pure white | The selling price will be USD30-50 Per ton |
2 | Crystallization and dry will be finished in one step The final moisture can be ≤50ppm | It will be a good point to next user, like the PET Preform manufacture, PET Sheet manufacture or Fiber manufacture etc. It will shorten their pre-drying time. |
3 | Complete machine controlled by Siemens PLC Touch screen with memory function, one key start. | To reduce the technique labour cost. |
4 | Save almost 45-50% energy cost compared with Dessicant dryer | Take 500kg/h Infrared crystal dryer model as example, the electrical cost is less than 100W/KG/HR |