Raw Material | PET Recycled flake/ PET sheet scrap/PET Preform scrap | ![]() |
Using Machine | LDHW-600*1000 | ![]() |
Drying& Crystallized Temperature set | 180-200℃Can be adjustable by property of rawmaterial | |
Crystallized time set | 20mins | |
Final material | Crystallized and Dried PET scraps and final moisture can be about 30ppm | ![]() |
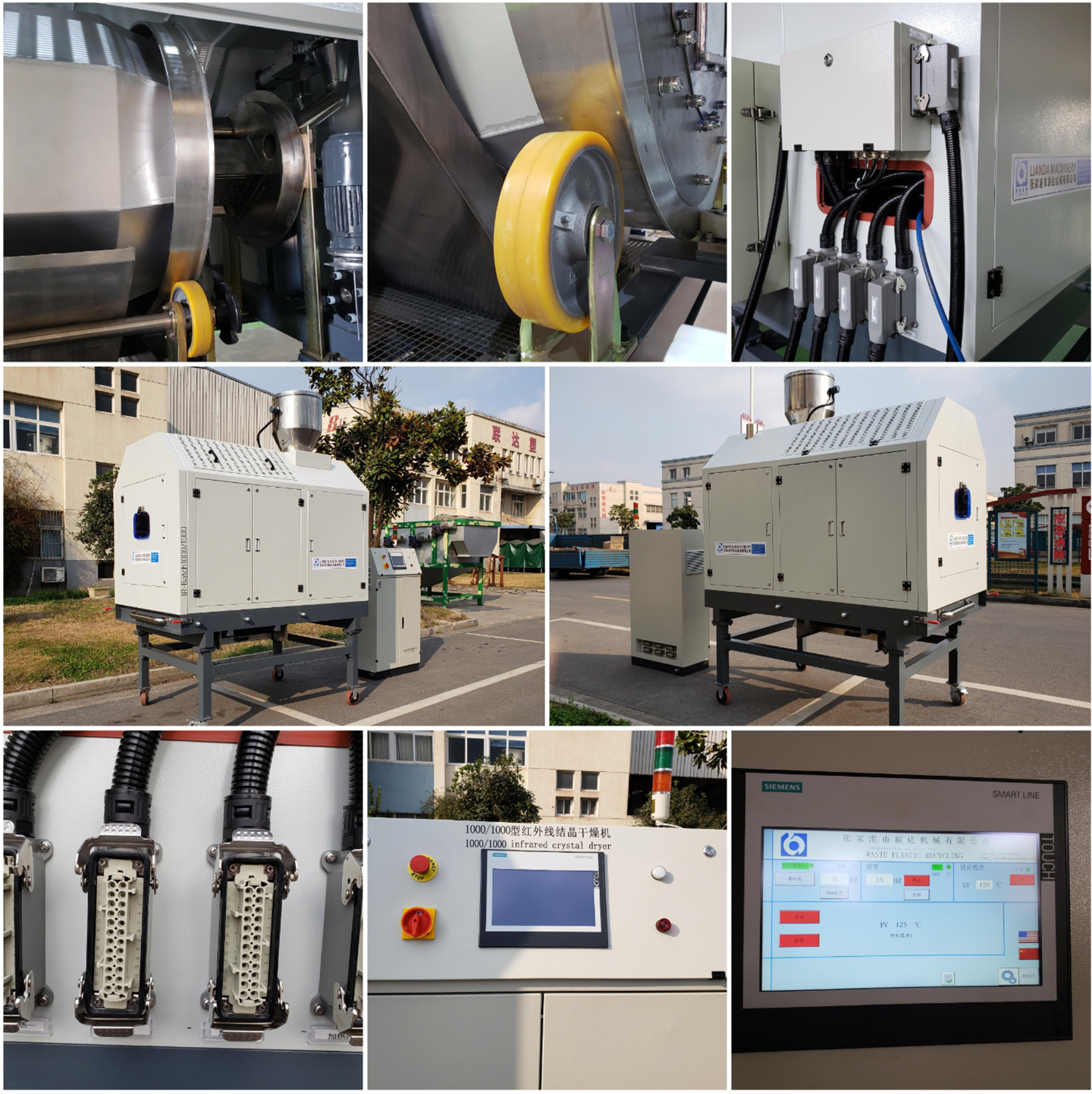
● Limiting the hydrolytic degradation of the viscosity. ● Prevent increasing AA levels for materials with food contact ● Increasing the capacity of the production line up to 50% ● Improvement and make the product quality stable-- Equal and repeatable input moisture content of the material
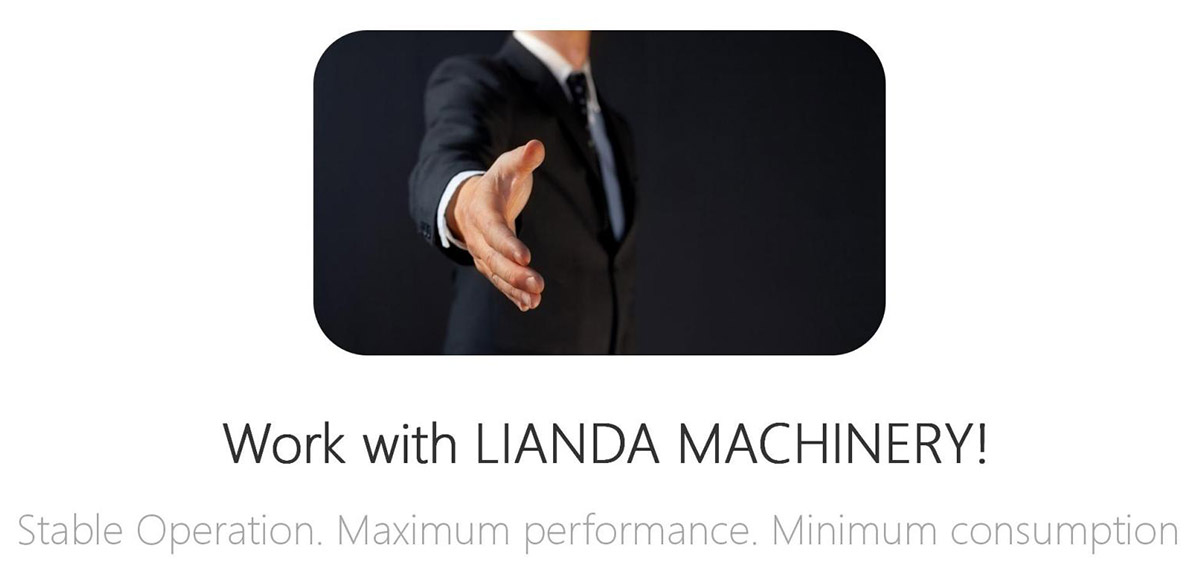
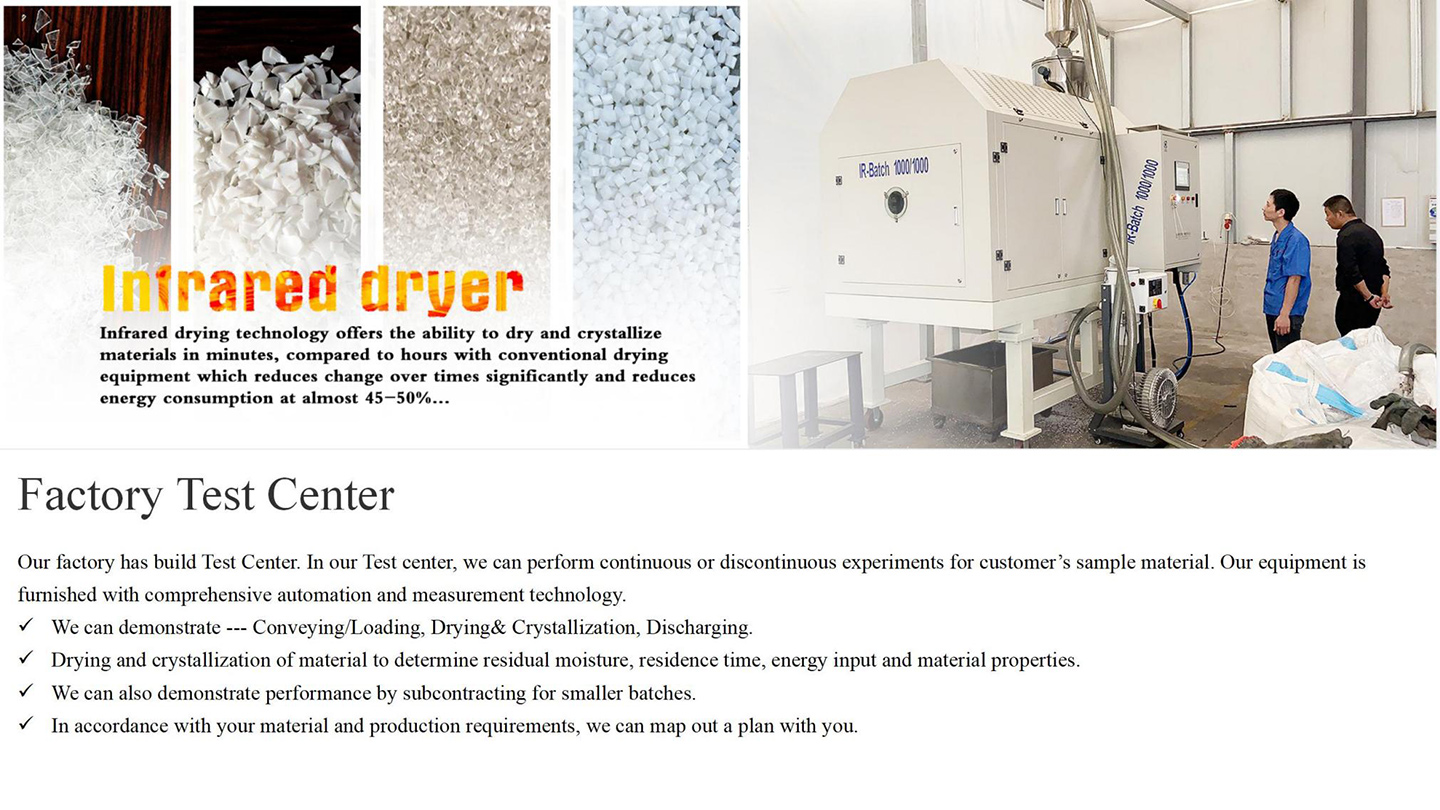
Item | IRD Dryer | Conventional Dryer |
Transfer medium | None | Hot air |
Heat transfer | Both inside & outside particles together. | From outside to inside particle gradually. |
Energy | Save at least 20~50% energy compared to traditional dryer. | Consume much energy. |
Process time | 1. Crystallization & drying: They are processed simultaneously within about 8~15 minutes. 2. Drying and crystallization at a time | 1. Crystallization: About 30~60 minutes. 2. Drying: About 4~6 hours. |
Moisturecontent | 1. Under 50-70 PPM after IRD processed. | 1. Spend 30~60 minutes to change amorphous PET to crystallized PET first. 2. Under 200PPM after about 4 hours dehumidifier processed. 3. Under 50 PPM after about more than 6 hours dehumidifier processed. |
Lead time | 20mins | More than 6 hours. |
Material changeover | 1. Easy & faster. 2. There are only 1~1.5 times capacity of material hourly consumption in the buffer hopper. | 1. Difficult & slowly. 2. There are 5~7 times capacity of material hourly consumption in the crystallizer & hopper. |
Operation | Simple--- By Siemens PLC control | It is difficult such as it must put a little crystallized PET in the crystallizer when beginning operation. |
Maintenance | 1. Simple. 2. Lower maintenance cost. | 1. Difficult. 2. Higher maintenance cost. |
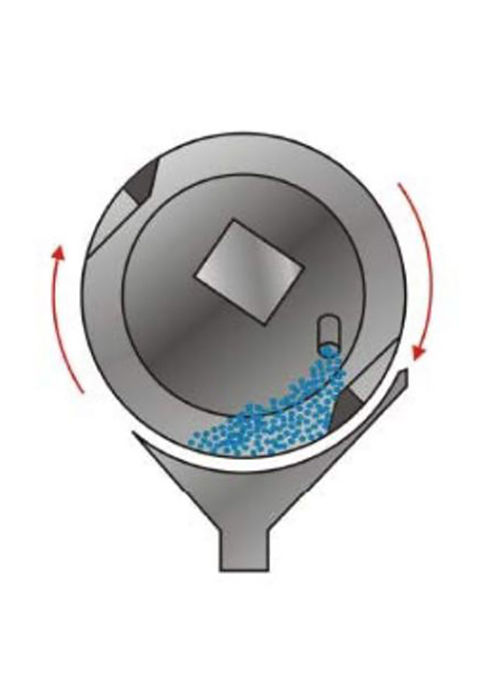
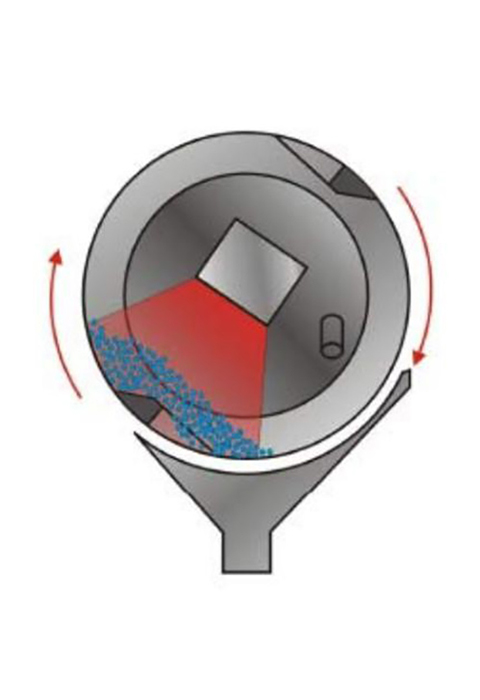
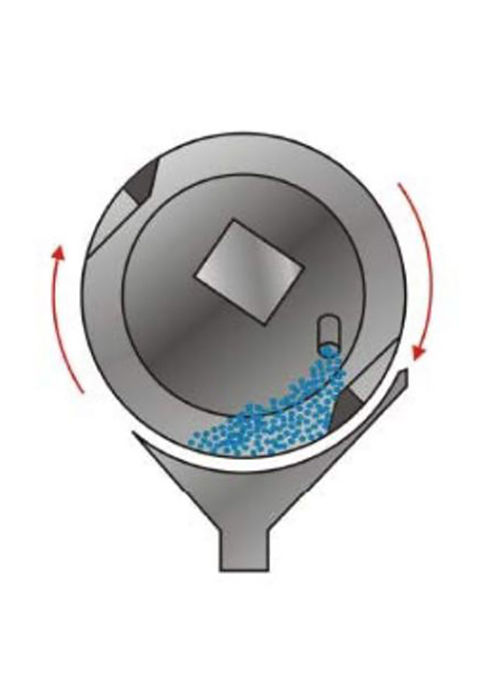